The Role Of Protective Coatings In Corrosion Prevention
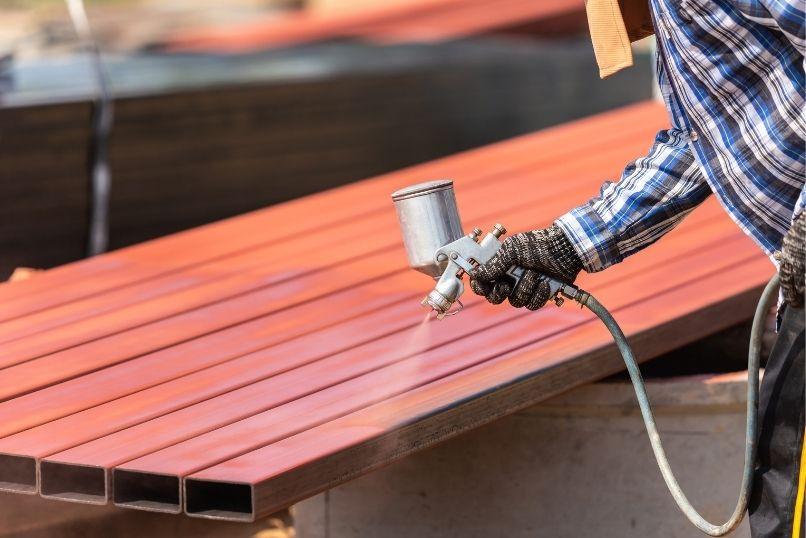
Corrosion is a pervasive problem that affects a wide range of industries, from infrastructure and transportation to energy production and manufacturing. It is a natural process that leads to the deterioration of materials, especially metals, due to chemical reactions with their environment. The consequences of corrosion are vast, including structural failures, safety hazards, and significant economic losses. One of the most effective methods to combat corrosion is the application of protective coatings. These coatings serve as barriers that isolate the material from its environment, thereby preventing or significantly slowing down the corrosion process.
In this comprehensive blog post, we will explore the role of protective coatings in corrosion prevention. We will delve into the different types of protective coatings, their mechanisms of action, application techniques, and the industries that rely heavily on these coatings. We will also discuss the challenges associated with protective coatings and the future trends in this critical area of corrosion prevention.
Understanding Corrosion: A Brief Overview
Corrosion is an electrochemical process that results in the degradation of materials, typically metals, through reactions with their environment. The most common form of corrosion is the oxidation of metals, where the metal reacts with oxygen and moisture to form oxides. For example, the rusting of iron involves the formation of iron oxide as iron reacts with oxygen in the presence of water.
The corrosion process involves two primary reactions: the anodic reaction, where the metal loses electrons and undergoes oxidation, and the cathodic reaction, where these electrons are consumed in a reduction process. The presence of an electrolyte, such as water, facilitates the movement of ions, completing the electrochemical circuit necessary for corrosion to occur.
Corrosion can take many forms, including uniform corrosion, pitting, crevice corrosion, galvanic corrosion, and stress corrosion cracking. Each type of corrosion presents unique challenges and requires specific strategies for prevention. One of the most widely used and effective strategies is the application of protective coatings.
Protective Coatings: An Overview
Protective coatings are materials applied to the surface of a substrate, typically metal, to protect it from environmental factors that can cause corrosion. These coatings act as a physical barrier, preventing contact between the substrate and corrosive agents such as water, oxygen, chemicals, and salts. By isolating the substrate from its environment, protective coatings can significantly reduce or eliminate the risk of corrosion.
Protective coatings can be classified into several categories based on their composition, function, and application method. The main types of protective coatings include:
-
Metallic Coatings
-
Organic Coatings
-
Inorganic Coatings
-
Conversion Coatings
Each type of coating has unique properties and applications, and the choice of coating depends on factors such as the substrate material, environmental conditions, and the desired level of protection.
Types of Protective Coatings
1. Metallic Coatings
Metallic coatings involve the application of a layer of metal onto the surface of a substrate to protect it from corrosion. These coatings can be applied using various methods, including electroplating, hot-dip galvanizing, thermal spraying, and cladding.
Examples of Metallic Coatings:
-
Zinc Coatings (Galvanizing): Zinc is one of the most commonly used metals for protective coatings, particularly for steel. Galvanizing involves immersing steel in molten zinc to form a protective layer. Zinc provides sacrificial protection, meaning it corrodes in place of the steel, thereby preventing rust formation. Galvanized steel is widely used in construction, automotive, and infrastructure applications.
-
Aluminum Coatings: Aluminum coatings are used to protect steel and other metals from corrosion, particularly in high-temperature environments. Aluminum forms a stable oxide layer that provides excellent resistance to corrosion. These coatings are commonly used in the aerospace and automotive industries.
-
Nickel and Chromium Coatings: Nickel and chromium coatings are often used for their decorative and protective properties. Nickel plating is widely used in the automotive and electronics industries, while chromium plating is used in applications where high corrosion resistance and a shiny appearance are required.
Mechanisms of Protection:
-
Barrier Protection: Metallic coatings provide a physical barrier that prevents corrosive agents from reaching the substrate. This barrier is effective as long as it remains intact and free of defects.
-
Sacrificial Protection: Some metallic coatings, such as zinc, offer sacrificial protection. The coating corrodes preferentially, protecting the underlying substrate from corrosion.
-
Cathodic Protection: In some cases, metallic coatings can provide cathodic protection by acting as a sacrificial anode. This is common in galvanic protection systems where the coated metal serves as the anode, protecting the substrate from corrosion.
2. Organic Coatings
Organic coatings are composed of organic compounds, primarily polymers, that are applied to the surface of a substrate to protect it from corrosion. These coatings are versatile, offering a wide range of protective properties, and are widely used in various industries.
Examples of Organic Coatings:
-
Paints: Paints are one of the most common types of organic coatings. They consist of pigments, binders, solvents, and additives. Paints are used to protect a wide range of substrates, including metals, wood, and concrete, from environmental factors such as moisture, UV radiation, and chemicals.
-
Epoxy Coatings: Epoxy coatings are known for their excellent adhesion, chemical resistance, and durability. They are widely used in industrial applications, such as pipelines, storage tanks, and marine environments, where high corrosion resistance is required.
-
Polyurethane Coatings: Polyurethane coatings offer excellent resistance to abrasion, chemicals, and UV radiation. They are commonly used in automotive, aerospace, and marine applications.
Mechanisms of Protection:
-
Barrier Protection: Organic coatings form a continuous, impermeable film that prevents corrosive agents from reaching the substrate. The effectiveness of this barrier depends on the coating's thickness, adhesion, and resistance to environmental factors.
-
Inhibitive Protection: Some organic coatings contain corrosion inhibitors that are released over time. These inhibitors react with the substrate or the environment to reduce the rate of corrosion.
-
Passivation: Certain organic coatings can passivate the substrate, reducing its reactivity and susceptibility to corrosion. This is often achieved by incorporating passivating agents into the coating formulation.
3. Inorganic Coatings
Inorganic coatings are composed of inorganic compounds, such as ceramics or metallic oxides, that provide excellent protection against corrosion, particularly in harsh environments. These coatings are known for their high temperature resistance, durability, and chemical stability.
Examples of Inorganic Coatings:
-
Ceramic Coatings: Ceramic coatings are used in high-temperature and chemically aggressive environments. They provide excellent resistance to oxidation, corrosion, and wear. Common applications include turbine blades, exhaust systems, and chemical processing equipment.
-
Zinc-Rich Primers: Zinc-rich primers are a type of inorganic coating that contains a high percentage of zinc powder. These coatings provide sacrificial protection to steel structures, similar to galvanizing, and are commonly used in marine, industrial, and infrastructure applications.
-
Silicate Coatings: Silicate coatings are inorganic coatings that provide excellent resistance to high temperatures, chemicals, and UV radiation. They are often used in industrial applications where exposure to harsh environments is a concern.
Mechanisms of Protection:
-
Barrier Protection: Inorganic coatings provide a highly resistant barrier that protects the substrate from corrosive agents. The durability and stability of these coatings make them ideal for extreme environments.
-
Chemical Resistance: Inorganic coatings are often chemically inert, providing protection in environments where organic coatings would degrade. This makes them suitable for use in chemical processing, marine, and high-temperature applications.
-
Sacrificial Protection: Zinc-rich primers provide sacrificial protection, similar to metallic zinc coatings. The zinc particles in the primer corrode preferentially, protecting the underlying steel from corrosion.
4. Conversion Coatings
Conversion coatings are formed by chemically altering the surface of the substrate to create a protective layer. These coatings are often used as pretreatments before applying other protective coatings, such as paints or powder coatings.
Examples of Conversion Coatings:
-
Phosphate Coatings: Phosphate coatings are formed by immersing the metal substrate in a phosphoric acid solution, which reacts with the metal to form a layer of insoluble metal phosphates. These coatings provide moderate corrosion resistance and are often used as a base for painting or powder coating.
-
Chromate Coatings: Chromate coatings are formed by applying a solution containing hexavalent chromium to the metal substrate. The chromate reacts with the metal to form a protective layer of chromium oxides and hydroxides. Chromate coatings are commonly used on aluminum and zinc substrates.
-
Anodizing: Anodizing is an electrochemical process used to create a thick oxide layer on the surface of aluminum and other metals. The anodized layer provides excellent corrosion resistance and can be further enhanced with dyes or sealants.
Mechanisms of Protection:
-
Surface Passivation: Conversion coatings passivate the substrate, reducing its reactivity and susceptibility to corrosion. This passivation effect is often used as a pretreatment before applying additional protective coatings.
-
Adhesion Promotion: Conversion coatings improve the adhesion of subsequent coatings, such as paints or powder coatings, by providing a rough, chemically bonded surface. This enhances the overall durability and corrosion resistance of the coated system.
-
Barrier Protection: Conversion coatings provide a protective barrier that reduces the permeability of the substrate to corrosive agents. This barrier is often thin and used in conjunction with other coatings for enhanced protection.
Application Techniques for Protective Coatings
The effectiveness of protective coatings depends not only on the choice of coating material but also on the application technique. Proper application ensures that the coating adheres well to the substrate, provides uniform coverage, and maintains its protective properties over time. Some common application techniques for protective coatings include:
1. Spray Coating
Spray coating involves the use of a spray gun to apply the coating material to the substrate. This technique is widely used for applying paints, primers, and other liquid coatings. Spray coating allows for even coverage and is suitable for large surfaces and complex geometries.
2. Brush and Roller Coating
Brush and roller coating is a manual application technique used for small areas or touch-up work. It is commonly used for applying paints and primers in areas where spray coating is impractical. While this technique is slower and may result in less uniform coverage, it allows for precise application in hard-to-reach areas.
3. Dip Coating
Dip coating involves immersing the substrate in a liquid coating material and then allowing the excess coating to drain off. This technique is used for applying uniform coatings to small parts, such as fasteners, or for applying thick coatings, such as plastisol or rubber coatings.
4. Electroplating
Electroplating is an electrochemical process used to deposit a layer of metal onto the substrate. The substrate is immersed in an electrolyte solution containing the metal ions to be plated, and an electric current is applied. Electroplating is commonly used for applying metallic coatings, such as nickel, chrome, or zinc.
5. Powder Coating
Powder coating involves the application of a dry, powdered coating material to the substrate, followed by curing in an oven. The powder is applied using an electrostatic spray gun, which imparts an electric charge to the powder particles, causing them to adhere to the substrate. Powder coating provides a durable, uniform finish and is commonly used in automotive, appliance, and industrial applications.
6. Hot-Dip Galvanizing
Hot-dip galvanizing involves immersing the steel substrate in molten zinc to form a thick, protective layer of zinc. This technique is widely used for protecting steel structures, such as bridges, guardrails, and utility poles, from corrosion. Hot-dip galvanizing provides long-lasting protection, even in harsh environments.
Industries that Rely on Protective Coatings
Protective coatings play a crucial role in various industries, where corrosion prevention is essential to maintain the integrity and safety of assets. Some of the key industries that rely on protective coatings include:
1. Oil and Gas Industry
The oil and gas industry is highly susceptible to corrosion due to the harsh environments in which it operates, including offshore platforms, pipelines, and refineries. Protective coatings are used extensively to protect equipment, structures, and pipelines from corrosion caused by seawater, chemicals, and high temperatures. Coatings such as epoxy, polyurethane, and zinc-rich primers are commonly used in this industry.
2. Marine Industry
The marine industry faces some of the most challenging corrosion conditions due to constant exposure to seawater, salt spray, and humidity. Protective coatings are essential for protecting ships, offshore structures, and marine equipment from corrosion. Anti-fouling coatings, which prevent the growth of marine organisms, are also commonly used in this industry.
3. Automotive Industry
Corrosion prevention is critical in the automotive industry to ensure the longevity and safety of vehicles. Protective coatings are used on various components, including body panels, chassis, and engine parts, to protect them from corrosion caused by moisture, road salts, and chemicals. Common coatings used in the automotive industry include paints, electrocoats, and underbody coatings.
4. Aerospace Industry
The aerospace industry requires protective coatings that can withstand extreme temperatures, UV radiation, and chemical exposure. Coatings are used to protect aircraft components, such as fuselage panels, landing gear, and engine parts, from corrosion and wear. High-performance coatings, such as ceramic coatings and epoxy primers, are commonly used in the aerospace industry.
5. Construction Industry
The construction industry relies on protective coatings to protect structures, such as bridges, buildings, and pipelines, from corrosion. Coatings are applied to steel and concrete to prevent deterioration caused by moisture, chemicals, and environmental factors. Common coatings used in construction include paints, epoxies, and galvanized coatings.
6. Water Treatment Industry
Corrosion prevention is critical in water treatment systems, where metal components are constantly exposed to water, dissolved salts, and chemicals. Protective coatings are used to protect pipes, tanks, and equipment from corrosion and scale formation. Common coatings used in water treatment include epoxy linings, zinc-rich primers, and polyurethane coatings.
Challenges and Future Trends in Protective Coatings
While protective coatings are highly effective in preventing corrosion, they also face several challenges. Some of the key challenges include:
-
Environmental and Health Concerns: Many traditional coatings contain volatile organic compounds (VOCs) and hazardous materials, which can pose environmental and health risks. The industry is increasingly moving toward the development of low-VOC and environmentally friendly coatings.
-
Coating Durability: The durability of protective coatings is critical to their effectiveness. Coatings must withstand harsh environmental conditions, mechanical wear, and chemical exposure without degrading over time.
-
Cost: The cost of protective coatings, including application and maintenance, can be significant. The industry is continually seeking cost-effective solutions that provide long-lasting protection.
-
Coating Adhesion: Proper adhesion to the substrate is essential for the effectiveness of protective coatings. Surface preparation, coating formulation, and application technique all play a role in ensuring strong adhesion.
Looking ahead, the future of protective coatings is likely to be shaped by advancements in materials science, nanotechnology, and environmental regulations. Some of the emerging trends in protective coatings include:
-
Smart Coatings: Smart coatings are designed to respond to environmental changes, such as temperature, moisture, or chemical exposure, by altering their properties. These coatings can provide self-healing, anti-fouling, or corrosion-inhibiting capabilities.
-
Nanocoatings: Nanotechnology is being used to develop coatings with enhanced properties, such as increased hardness, chemical resistance, and UV protection. Nanocoatings have the potential to provide superior protection in a wide range of applications.
-
Green Coatings: The development of environmentally friendly coatings that are free of hazardous materials and VOCs is a growing trend. Green coatings are designed to meet stringent environmental regulations while providing effective corrosion protection.
-
Hybrid Coatings: Hybrid coatings combine the benefits of different coating materials, such as organic and inorganic components, to provide enhanced protection. These coatings offer a balance of barrier, chemical resistance, and mechanical properties.
Conclusion
Protective coatings play a vital role in corrosion prevention, offering a practical and cost-effective solution to protect materials from the damaging effects of corrosion. By forming a barrier between the substrate and the corrosive environment, these coatings can significantly extend the life of structures, equipment, and components across various industries.
The choice of protective coating depends on several factors, including the substrate material, environmental conditions, and the specific application. Understanding the different types of coatings, their mechanisms of protection, and their application techniques is essential for selecting the most appropriate coating for each situation.
As technology advances, the development of new and more effective protective coatings will continue to play a crucial role in addressing the challenges of corrosion in increasingly complex and demanding environments. Whether in protecting critical infrastructure, enhancing the safety and performance of vehicles and aircraft, or ensuring the integrity of pipelines and storage tanks, protective coatings will remain at the forefront of corrosion prevention and control.