Introduction To Corrosion: Types, Causes, And Prevention
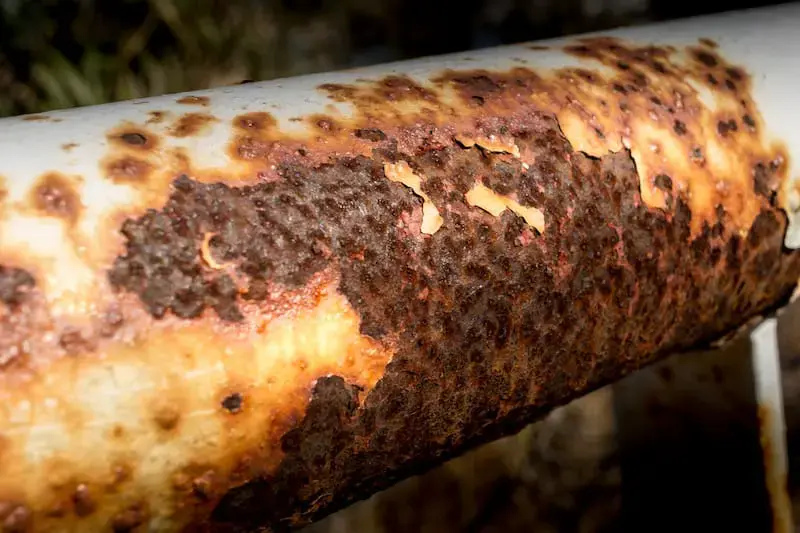
Corrosion is a pervasive and persistent problem that affects a wide range of industries, from oil and gas to construction and transportation. It is a natural process that leads to the gradual destruction of materials, particularly metals, due to chemical reactions with their environment. The economic impact of corrosion is significant, costing industries billions of dollars annually in maintenance, repair, and replacement. Beyond the financial implications, corrosion can also pose serious safety risks, leading to structural failures, leaks, and even catastrophic accidents.
Understanding corrosion, its causes, the various types, and effective prevention methods is essential for engineers, scientists, and maintenance professionals. This blog post provides a comprehensive overview of corrosion, exploring its types, underlying causes, and the strategies employed to prevent or mitigate its effects.
What is Corrosion?
Corrosion is the degradation of a material, usually a metal, as a result of chemical or electrochemical reactions with its environment. The most common form of corrosion is the oxidation of metals, where metal atoms lose electrons and form oxides or other compounds. This process is most familiar in the rusting of iron and steel, but it can affect almost all metals, including aluminum, copper, and zinc.
Corrosion is a natural process driven by the tendency of metals to revert to their more stable, lower-energy oxidized states. While corrosion can sometimes be beneficial, such as in the formation of a protective oxide layer on aluminum, it is generally an undesirable process that compromises the integrity, functionality, and aesthetic of the affected material.
Types of Corrosion
Corrosion manifests in various forms, each with distinct characteristics and mechanisms. Understanding the different types of corrosion is crucial for diagnosing issues and implementing appropriate prevention and mitigation strategies. Below are the most common types of corrosion:
1. Uniform Corrosion
Uniform corrosion, also known as general corrosion, occurs uniformly over the entire surface of a material. This type of corrosion is the most predictable and can often be anticipated and managed. It typically results in a gradual thinning of the material, which can be monitored and measured over time. For example, the rusting of an iron or steel surface in a humid environment is a typical case of uniform corrosion.
Prevention:
-
Applying protective coatings such as paints, plating, or galvanizing can significantly reduce the rate of uniform corrosion.
-
Regular maintenance and inspections to detect and address early signs of corrosion.
2. Galvanic Corrosion
Galvanic corrosion occurs when two dissimilar metals are in electrical contact in the presence of an electrolyte, such as water. The more active metal (anode) corrodes faster, while the less active metal (cathode) is protected. This type of corrosion is common in situations where different metals are joined together, such as in piping systems or marine environments.
Prevention:
-
Avoiding the use of dissimilar metals in direct contact, or using insulating materials to separate them.
-
Using sacrificial anodes, such as zinc, to protect the more critical metal components.
3. Pitting Corrosion
Pitting corrosion is a localized form of corrosion that leads to the formation of small, often hard-to-detect pits or holes on the surface of a material. It is one of the most insidious types of corrosion because it can cause significant damage with minimal material loss. Pitting is particularly dangerous because it can lead to the perforation of metal surfaces, causing leaks or structural failures.
Prevention:
-
Using materials that are less prone to pitting, such as high-quality stainless steel.
-
Ensuring that protective coatings are intact and free from defects.
-
Controlling environmental factors, such as chloride concentration in water, which can exacerbate pitting.
4. Crevice Corrosion
Crevice corrosion occurs in confined spaces where the access of oxygen is restricted, such as under gaskets, seals, or in sharp corners and seams. The corrosion process begins when the oxygen concentration inside the crevice drops, creating a differential in the electrochemical potential between the crevice and the surrounding areas. This leads to aggressive localized corrosion within the crevice.
Prevention:
-
Designing components to minimize crevices, seams, and gaps where corrosion can initiate.
-
Using non-absorbent gaskets and seals to reduce the likelihood of moisture retention.
-
Regular cleaning and inspection of potential crevice areas.
5. Intergranular Corrosion
Intergranular corrosion occurs along the grain boundaries of a metal, often due to the presence of impurities or the depletion of corrosion-resistant elements, such as chromium in stainless steel. This type of corrosion can cause a material to crumble along its grain boundaries, leading to structural failure even though the bulk material may remain unaffected.
Prevention:
-
Using low-carbon or stabilized grades of stainless steel that are less susceptible to intergranular attack.
-
Proper heat treatment processes, such as annealing, to eliminate or reduce the formation of susceptible grain boundaries.
6. Stress Corrosion Cracking (SCC)
Stress corrosion cracking is a type of corrosion that occurs when a material is subjected to tensile stress in a corrosive environment. SCC leads to the formation of cracks that propagate over time, potentially leading to catastrophic failures. SCC is particularly dangerous because it often occurs without significant visible corrosion, making it difficult to detect until failure is imminent.
Prevention:
-
Reducing or eliminating tensile stresses through proper design and material selection.
-
Using corrosion inhibitors or protective coatings to mitigate the corrosive environment.
-
Regular non-destructive testing (NDT) to detect early signs of cracking.
7. Erosion Corrosion
Erosion corrosion occurs when a material is subjected to a corrosive fluid that flows at a high velocity. The combined effects of mechanical wear and chemical attack lead to accelerated material loss, often resulting in the thinning of pipes, impellers, or other components exposed to flowing fluids. Erosion corrosion is common in pipelines, heat exchangers, and turbines.
Prevention:
-
Reducing fluid velocity and turbulence in design to minimize mechanical wear.
-
Using erosion-resistant materials, such as stainless steel or specialized alloys.
-
Implementing proper maintenance and inspection schedules to detect early signs of erosion corrosion.
8. Selective Leaching
Selective leaching, also known as dealloying, occurs when one element is selectively removed from an alloy, leaving behind a porous and weakened structure. A common example is the dezincification of brass, where zinc is leached out, leaving behind a brittle copper-rich residue. This type of corrosion can severely compromise the mechanical integrity of the material.
Prevention:
-
Using alloys that are less susceptible to selective leaching, such as dezincification-resistant brass.
-
Applying protective coatings to prevent exposure to corrosive environments.
-
Controlling the composition of the operating environment to reduce the risk of leaching.
9. Hydrogen Embrittlement
Hydrogen embrittlement occurs when hydrogen atoms diffuse into a metal, causing it to become brittle and prone to cracking. This type of corrosion is particularly problematic in high-strength steels, which can lose their ductility and toughness due to the presence of hydrogen. Hydrogen embrittlement is a concern in environments where hydrogen is present, such as during electroplating or in hydrogen-rich atmospheres.
Prevention:
-
Using materials with low susceptibility to hydrogen embrittlement.
-
Controlling environmental conditions to minimize hydrogen exposure, such as using proper plating techniques or avoiding contact with hydrogen-rich environments.
-
Implementing post-process treatments, such as baking, to remove absorbed hydrogen.
10. Corrosion Fatigue
Corrosion fatigue occurs when a material is subjected to cyclic stresses in a corrosive environment. The combination of mechanical fatigue and corrosion leads to the initiation and propagation of cracks, which can ultimately cause failure. Corrosion fatigue is a significant concern in components subjected to fluctuating loads, such as aircraft parts, bridges, and rotating machinery.
Prevention:
-
Reducing cyclic stresses through proper design and material selection.
-
Using corrosion-resistant materials or protective coatings to mitigate the corrosive environment.
-
Implementing regular inspection and maintenance schedules to detect early signs of fatigue.
Causes of Corrosion
Corrosion is driven by several factors that interact in complex ways. Understanding these causes is crucial for developing effective prevention and mitigation strategies. The primary causes of corrosion include:
1. Environmental Factors
The environment plays a significant role in the corrosion process. Key environmental factors include:
-
Moisture and Humidity: Water is a primary catalyst for many corrosion processes. The presence of moisture in the air or direct contact with water can accelerate corrosion, especially in metals like iron and steel.
-
Oxygen: Oxygen is essential for the oxidation process that drives most forms of corrosion. The availability of oxygen, particularly in the presence of water, can significantly increase the rate of corrosion.
-
Temperature: Higher temperatures can accelerate the chemical reactions involved in corrosion, leading to faster material degradation.
-
Chlorides and Salts: Chloride ions, commonly found in seawater and de-icing salts, are particularly aggressive in promoting corrosion, especially in metals like stainless steel.
-
pH Levels: The acidity or alkalinity of the environment can influence the rate of corrosion. Acidic environments (low pH) are particularly corrosive to metals.
2. Material Properties
The inherent properties of a material can influence its susceptibility to corrosion. Key material factors include:
-
Composition: The chemical composition of a material determines its corrosion resistance. For example, stainless steel contains chromium, which forms a protective oxide layer, making it more resistant to corrosion.
-
Microstructure: The microstructure of a material, including grain size and phase distribution, can affect its corrosion behavior. Materials with certain microstructures may be more prone to intergranular or pitting corrosion.
-
Surface Condition: The condition of the material’s surface, including roughness, coatings, and cleanliness, can significantly impact its corrosion resistance.
3. Mechanical Stresses
Mechanical stresses, including tensile, compressive, and cyclic stresses, can exacerbate corrosion by creating conditions that promote crack initiation and propagation. For example, stress corrosion cracking occurs when a material is subjected to tensile stress in a corrosive environment, leading to the formation of cracks.
4. Electrochemical Reactions
Corrosion is fundamentally an electrochemical process, involving the transfer of electrons between the metal and its environment. The electrochemical nature of corrosion is influenced by factors such as:
-
Electrode Potential: The difference in potential between anodic and cathodic areas on a metal surface drives the corrosion process. Metals with higher electrode potentials are more likely to corrode in the presence of a suitable electrolyte.
-
Electrolytes: The presence of an electrolyte, such as water or an aqueous solution, is essential for the electrochemical reactions involved in corrosion. Electrolytes facilitate the movement of ions, which is critical for the corrosion process.
Prevention of Corrosion
Preventing or mitigating corrosion is a key concern in industries where material longevity and structural integrity are critical. Various strategies can be employed to reduce the risk of corrosion, each tailored to the specific type of corrosion and the environmental conditions involved. Below are some common corrosion prevention methods:
1. Material Selection
Choosing the right material is one of the most effective ways to prevent corrosion. Materials with inherent corrosion resistance, such as stainless steel, titanium, and certain alloys, can withstand harsh environments better than more susceptible materials. Material selection should consider factors such as:
-
Corrosive Environment: Understanding the specific environmental conditions, such as the presence of chlorides, moisture, or acidic conditions, is essential for selecting an appropriate material.
-
Mechanical Requirements: The material must meet the mechanical demands of the application, including strength, ductility, and toughness, without compromising corrosion resistance.
2. Protective Coatings
Applying protective coatings is a common method for preventing corrosion. Coatings act as a barrier between the material and its environment, preventing the exposure of the underlying metal to corrosive agents. Common types of protective coatings include:
-
Paints and Varnishes: Organic coatings that provide a physical barrier against moisture and oxygen.
-
Plating: Electroplating metals like zinc, nickel, or chrome onto a surface to enhance corrosion resistance.
-
Galvanizing: Coating steel with a layer of zinc to protect against rusting. The zinc acts as a sacrificial anode, corroding in place of the steel.
-
Powder Coating: A dry coating process that provides a durable, corrosion-resistant finish.
3. Cathodic Protection
Cathodic protection is a technique used to prevent corrosion by converting the entire metal surface into a cathode of an electrochemical cell. There are two primary methods of cathodic protection:
-
Sacrificial Anode: Attaching a more reactive metal (sacrificial anode) to the structure. The sacrificial anode corrodes preferentially, protecting the main structure.
-
Impressed Current: Applying an external current to counteract the corrosion current, thus protecting the structure. This method is commonly used in large structures like pipelines and storage tanks.
4. Corrosion Inhibitors
Corrosion inhibitors are chemicals added to the environment to reduce the rate of corrosion. These inhibitors work by:
-
Forming a Protective Film: Inhibitors can form a thin protective film on the metal surface, preventing corrosive agents from reaching the metal.
-
Neutralizing Acids: Inhibitors can neutralize acidic conditions in the environment, reducing the corrosive potential.
-
Reducing Oxidation: Inhibitors can interfere with the electrochemical reactions that lead to oxidation, thus slowing the corrosion process.
5. Design Modifications
Good design practices can significantly reduce the risk of corrosion. Design modifications can include:
-
Avoiding Crevices: Designing components to eliminate or minimize crevices where moisture and corrosive agents can accumulate.
-
Proper Drainage: Ensuring that structures and components have adequate drainage to prevent water accumulation.
-
Reducing Stress Concentrations: Designing components to avoid sharp corners and sudden changes in cross-section, which can create stress concentrations and promote stress corrosion cracking.
6. Environmental Control
Controlling the environment is another effective strategy for preventing corrosion. Environmental control methods can include:
-
Humidity Control: Reducing humidity levels in storage and operating environments can significantly reduce the risk of corrosion, especially for metals prone to rusting.
-
Temperature Control: Maintaining stable temperatures and avoiding excessive heat can prevent accelerated corrosion rates.
-
Chemical Treatment: Treating the environment with chemicals, such as corrosion inhibitors or pH adjusters, can reduce the corrosive potential.
7. Regular Maintenance and Inspection
Regular maintenance and inspection are crucial for detecting and addressing corrosion before it leads to significant damage. Maintenance activities can include:
-
Cleaning: Regular cleaning to remove corrosive agents, such as salts, dirt, and moisture, from surfaces.
-
Inspection: Conducting regular inspections, including visual inspections and non-destructive testing (NDT), to detect early signs of corrosion.
-
Repair and Recoating: Promptly repairing any damaged coatings and recoating surfaces as needed to maintain protection.
Conclusion
Corrosion is a complex and multifaceted problem that affects various industries, leading to significant economic costs and safety risks. Understanding the different types of corrosion, their causes, and effective prevention methods is crucial for engineers, maintenance professionals, and decision-makers. By implementing appropriate material selection, protective coatings, cathodic protection, corrosion inhibitors, design modifications, environmental control, and regular maintenance, the risks associated with corrosion can be significantly reduced.
Ultimately, the goal of corrosion engineering is not just to prevent corrosion but to manage it effectively, ensuring the longevity, safety, and reliability of critical infrastructure and components. As industries continue to evolve and face new challenges, the importance of corrosion prevention and control will only grow, making it an essential area of focus for future innovation and development.