High-Temperature Corrosion: Causes, Effects, And Prevention
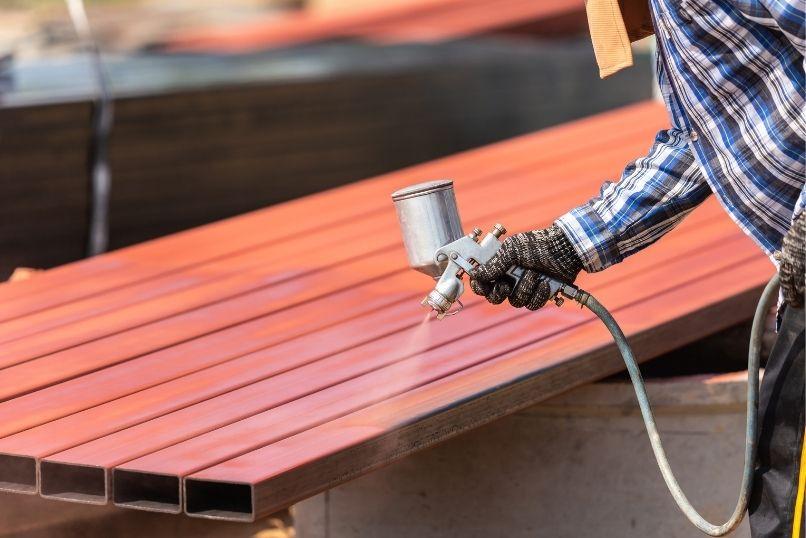
High-temperature corrosion is a significant challenge in industries that operate under extreme conditions, such as power generation, aerospace, and petrochemical processing. Unlike typical corrosion that occurs at lower temperatures, high-temperature corrosion involves complex chemical reactions between materials and their environment at elevated temperatures. These reactions can lead to rapid material degradation, affecting the structural integrity, performance, and lifespan of critical components.
This blog post delves into the causes, effects, and prevention strategies for high-temperature corrosion, offering insights into how industries can mitigate its impact and ensure the reliability of their operations.
Understanding High-Temperature Corrosion
High-temperature corrosion occurs when materials are exposed to high temperatures in the presence of corrosive environments, such as oxidizing, sulfidizing, or carburizing atmospheres. At these elevated temperatures, metals and alloys can react with various elements or compounds in the environment, leading to the formation of oxides, sulfides, carbides, or other compounds on the material's surface.
Key Factors Influencing High-Temperature Corrosion
-
Temperature: The temperature at which corrosion occurs plays a crucial role in determining the rate and type of corrosion. As temperature increases, the rate of chemical reactions typically increases, leading to accelerated corrosion. Different materials have varying temperature thresholds beyond which high-temperature corrosion becomes significant.
-
Environment: The composition of the surrounding environment, including the presence of oxygen, sulfur, carbon, chlorine, or other reactive species, determines the type of high-temperature corrosion that occurs. For example, environments rich in oxygen lead to oxidation, while those with sulfur lead to sulfidation.
-
Material Composition: The chemical composition of the material being used is a critical factor in determining its resistance to high-temperature corrosion. Alloys with specific elements, such as chromium, nickel, or aluminum, are often used because they can form protective oxide layers that slow down the corrosion process.
-
Time: The duration of exposure to high temperatures also affects the extent of corrosion. Prolonged exposure allows more time for chemical reactions to occur, leading to more significant material degradation.
Types of High-Temperature Corrosion
High-temperature corrosion can manifest in various forms depending on the environment and material involved. The most common types include:
1. Oxidation
Oxidation is one of the most prevalent forms of high-temperature corrosion. It occurs when metals react with oxygen at elevated temperatures, leading to the formation of metal oxides on the surface. While a thin oxide layer can protect the underlying metal, excessive oxidation can lead to the spalling of the oxide layer, exposing fresh metal to further corrosion.
-
Protective Oxide Formation: Some metals, like aluminum and chromium, form stable and adherent oxide layers (alumina and chromia) that protect the material from further oxidation.
-
Non-Protective Oxide Formation: Other metals, such as iron, may form non-protective oxide layers (like Fe2O3) that can spall off, leading to continuous material loss.
2. Sulfidation
Sulfidation occurs in environments containing sulfur or sulfur compounds, such as hydrogen sulfide (H2S). This form of corrosion leads to the formation of metal sulfides on the material's surface. Sulfidation is particularly aggressive at high temperatures and can cause rapid degradation of metal components, especially in the absence of protective oxide layers.
-
Hot Corrosion: A severe form of sulfidation, often referred to as "hot corrosion," occurs in environments where both sulfur and oxygen are present. It can lead to catastrophic material failure in components such as gas turbine blades.
3. Carburization
Carburization happens when metals are exposed to carbon-rich environments at high temperatures, leading to the absorption of carbon into the metal. This process results in the formation of carbides, which can embrittle the material and reduce its mechanical strength.
-
Metal Dusting: A particular form of carburization, known as metal dusting, occurs when carbon forms fine particles or "dust" that erodes the metal's surface, leading to significant material loss.
4. Chlorination
Chlorination occurs in environments containing chlorine or chlorine compounds, such as hydrochloric acid (HCl). This form of corrosion can lead to the formation of volatile metal chlorides, which can evaporate and cause material loss, especially at high temperatures.
-
Molten Salt Corrosion: In some high-temperature environments, molten salts containing chlorides can form, leading to aggressive corrosion and pitting on the metal surface.
Effects of High-Temperature Corrosion
The effects of high-temperature corrosion are far-reaching and can significantly impact the performance, safety, and longevity of industrial equipment and components.
1. Material Degradation
High-temperature corrosion leads to the gradual degradation of materials, resulting in the thinning of metal components, loss of mechanical strength, and eventual failure. This degradation can be particularly detrimental in critical applications, such as turbine blades, heat exchangers, and reactor vessels, where material integrity is essential for safe operation.
2. Mechanical Property Changes
Exposure to high temperatures and corrosive environments can alter the mechanical properties of materials. For example, carburization can cause embrittlement, making the material more susceptible to cracking under stress. Similarly, oxidation and sulfidation can reduce the ductility and toughness of metals, leading to premature failure under load.
3. Reduced Efficiency
In many industrial applications, high-temperature corrosion can lead to reduced efficiency. For example, corrosion of turbine blades in gas turbines can reduce aerodynamic efficiency, leading to lower power output and increased fuel consumption. Similarly, fouling of heat exchangers due to corrosion can reduce heat transfer efficiency, leading to higher operational costs.
4. Safety Risks
Perhaps the most significant effect of high-temperature corrosion is the increased risk of catastrophic failures. The sudden failure of critical components, such as pressure vessels, pipelines, or structural supports, can lead to accidents, environmental damage, and loss of life. The potential for such failures makes high-temperature corrosion a critical safety concern in many industries.
Prevention Strategies for High-Temperature Corrosion
Preventing high-temperature corrosion requires a comprehensive approach that includes material selection, protective coatings, environmental control, and regular maintenance. The following are some of the most effective strategies for mitigating high-temperature corrosion:
1. Material Selection
Selecting the right materials for high-temperature applications is the first line of defense against corrosion. Materials should be chosen based on their ability to resist the specific type of corrosion expected in the operating environment.
-
High-Temperature Alloys: Alloys containing chromium, nickel, and aluminum are commonly used in high-temperature applications because they can form stable, protective oxide layers. For example, stainless steels and superalloys are often used in gas turbines, heat exchangers, and chemical reactors.
-
Ceramic Materials: In extremely high-temperature environments, ceramic materials such as silicon carbide (SiC) and alumina (Al2O3) are used due to their excellent resistance to oxidation, sulfidation, and carburization.
2. Protective Coatings
Applying protective coatings to metal surfaces is an effective way to prevent high-temperature corrosion. These coatings can act as a barrier between the metal and the corrosive environment, reducing the rate of corrosion.
-
Thermal Barrier Coatings (TBCs): TBCs are commonly used in high-temperature applications, such as gas turbines, to protect metal components from oxidation and thermal degradation. These coatings typically consist of a ceramic topcoat that provides thermal insulation and a metallic bond coat that resists oxidation.
-
Aluminizing and Chromizing: Aluminizing and chromizing are processes that involve the diffusion of aluminum or chromium into the surface of the metal, forming a protective oxide layer. These coatings are particularly effective in preventing oxidation and sulfidation.
-
Corrosion-Resistant Paints: In some cases, high-temperature-resistant paints containing zinc, aluminum, or other corrosion inhibitors are used to protect metal surfaces from oxidation and other forms of corrosion.
3. Environmental Control
Controlling the environment in which materials operate is another important strategy for preventing high-temperature corrosion.
-
Atmosphere Control: In controlled environments, the composition of the atmosphere can be adjusted to minimize corrosive elements. For example, reducing the oxygen or sulfur content in a furnace atmosphere can significantly reduce the rate of oxidation or sulfidation.
-
Inert Gas Blanketing: In some applications, inert gases such as nitrogen or argon are used to blanket metal surfaces, preventing exposure to corrosive elements like oxygen, sulfur, or chlorine.
4. Design Considerations
Designing equipment and components with corrosion prevention in mind can help reduce the risk of high-temperature corrosion.
-
Avoiding Crevices and Gaps: Crevices and gaps can trap corrosive elements, leading to localized corrosion. Design strategies that minimize these features can reduce the risk of high-temperature corrosion.
-
Thermal Management: Proper thermal management can help control the temperature of critical components, reducing the risk of corrosion. For example, the use of cooling systems in gas turbines can help maintain blade temperatures below critical thresholds, reducing the rate of oxidation.
5. Regular Maintenance and Inspection
Regular maintenance and inspection are essential for detecting and addressing high-temperature corrosion before it leads to failure.
-
Non-Destructive Testing (NDT): Techniques such as ultrasonic testing, radiography, and eddy current testing can be used to detect early signs of corrosion, allowing for timely intervention.
-
Replacement and Repair: Components that show significant signs of high-temperature corrosion should be replaced or repaired to prevent catastrophic failures. In some cases, re-coating or surface treatment may be sufficient to restore the component's integrity.
Case Studies and Real-World Applications
Understanding the real-world impact of high-temperature corrosion and the effectiveness of prevention strategies can be further illustrated through case studies from various industries.
1. Gas Turbines in Power Generation
Gas turbines operate at extremely high temperatures, making them susceptible to oxidation, sulfidation, and hot corrosion. In one case study, the use of thermal barrier coatings and high-temperature alloys in a power plant significantly extended the life of turbine blades, reducing maintenance costs and improving overall efficiency.
2. Petrochemical Industry
In the petrochemical industry, reactors and pipelines are often exposed to sulfur-containing environments at high temperatures, leading to sulfidation. By selecting chromium-rich alloys and implementing strict atmosphere control, one refinery was able to reduce the rate of sulfidation, extending the lifespan of critical components.
3. Aerospace Applications
The aerospace industry faces unique challenges related to high-temperature corrosion, particularly in jet engines. By using advanced superalloys and protective coatings, aerospace engineers have been able to develop engines that can withstand the extreme conditions of flight, ensuring safety and reliability.
Conclusion
High-temperature corrosion is a complex and challenging phenomenon that affects a wide range of industries. By understanding the causes and effects of high-temperature corrosion, engineers and material scientists can develop effective strategies for prevention, ensuring the longevity, efficiency, and safety of critical infrastructure and equipment.
From material selection to protective coatings and environmental control, the strategies outlined in this post offer a comprehensive approach to combating high-temperature corrosion. As industries continue to push the boundaries of what is possible in terms of temperature and performance, the need for robust corrosion prevention measures will only grow. By staying ahead of the curve, industries can protect their assets, reduce costs, and maintain the highest standards of safety and reliability.