Corrosion Monitoring Techniques: From Sensors To Predictive Analytics
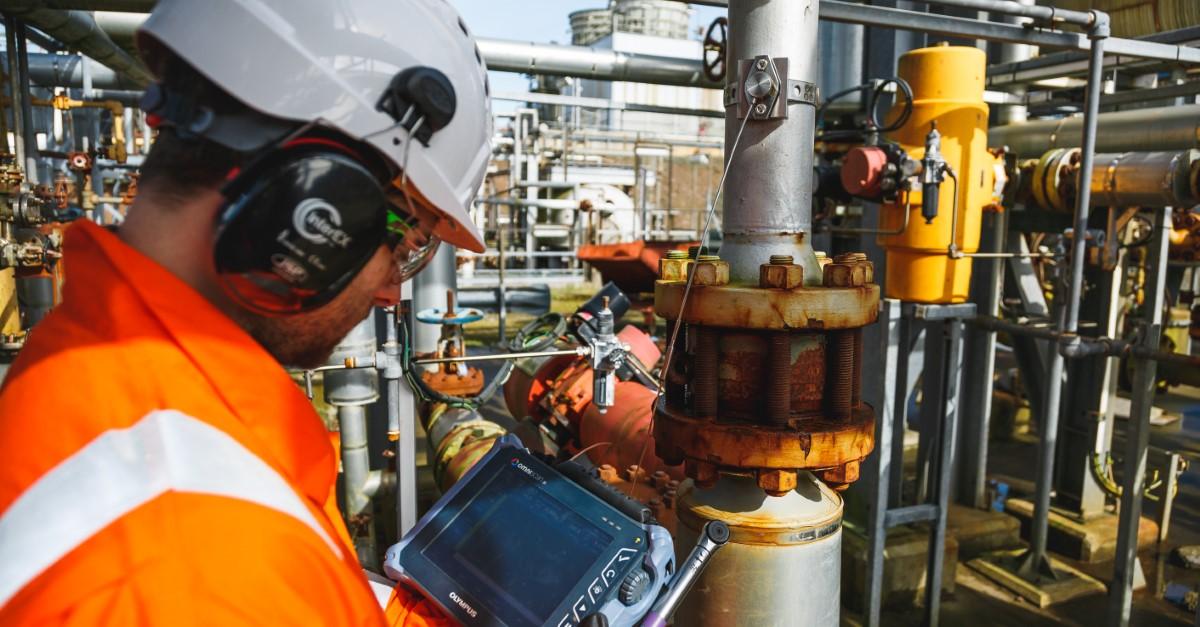
Corrosion is a persistent and costly problem that affects various industries, from oil and gas to transportation and infrastructure. As a natural process that deteriorates materials over time, corrosion poses significant challenges in terms of safety, reliability, and economic impact. Early detection and accurate monitoring are essential to preventing catastrophic failures and minimizing maintenance costs. In recent years, the field of corrosion monitoring has evolved dramatically, thanks to advancements in sensor technology and the emergence of predictive analytics.
This blog post explores the evolution of corrosion monitoring techniques, from traditional methods to cutting-edge technologies that leverage sensors and predictive analytics to provide more accurate and timely insights.
Understanding Corrosion and Its Impact
Corrosion is an electrochemical reaction that occurs when metals interact with their environment, leading to their gradual degradation. This process can be accelerated by factors such as moisture, salt, chemicals, and temperature fluctuations. The consequences of unchecked corrosion are far-reaching, including structural failures, environmental contamination, and financial losses. For example, the corrosion of pipelines can result in leaks or spills, while corrosion in bridges and buildings can compromise their structural integrity.
Given the serious implications of corrosion, effective monitoring is crucial. Monitoring techniques have traditionally relied on visual inspections and manual testing methods, which, while useful, have limitations in terms of accuracy, frequency, and the ability to detect corrosion at an early stage.
Traditional Corrosion Monitoring Techniques
1. Visual Inspection
Visual inspection is one of the oldest and most straightforward methods of corrosion monitoring. It involves a trained inspector examining the surface of a structure for signs of corrosion, such as rust, discoloration, or pitting. While this method is cost-effective and easy to perform, it has significant drawbacks. Visual inspections are inherently subjective, dependent on the inspector's experience and skill, and are often limited to accessible areas. This means that early-stage corrosion, which might not be visible to the naked eye, can go undetected.
2. Ultrasonic Testing
Ultrasonic testing (UT) is a non-destructive technique that uses high-frequency sound waves to detect internal defects in materials. In the context of corrosion monitoring, UT is used to measure the thickness of metal structures, allowing for the detection of thinning caused by corrosion. This method is highly accurate and can detect corrosion even in its early stages. However, ultrasonic testing requires skilled operators and can be time-consuming, especially when monitoring large structures.
3. Radiographic Testing
Radiographic testing (RT) uses X-rays or gamma rays to create images of the internal structure of a material. This technique is particularly useful for detecting corrosion in areas that are not accessible for visual inspection or ultrasonic testing, such as inside pipelines or within concrete. While radiographic testing is effective, it is also expensive and requires specialized equipment and safety precautions due to the use of radiation.
4. Electrochemical Methods
Electrochemical methods, such as linear polarization resistance (LPR) and electrochemical impedance spectroscopy (EIS), are used to measure the rate of corrosion by analyzing the electrical properties of the material. These techniques are highly sensitive and can provide real-time data on corrosion rates. However, they require contact with the material being tested and can be affected by environmental factors, making them less suitable for certain applications.
Advancements in Corrosion Monitoring: The Role of Sensors
In recent years, the development of advanced sensors has revolutionized the field of corrosion monitoring. These sensors provide continuous, real-time data on the condition of structures, enabling more accurate and timely detection of corrosion.
1. Corrosion Sensors
Corrosion sensors are devices specifically designed to detect the presence and rate of corrosion. These sensors can be embedded within structures or attached to the surface, where they monitor key parameters such as moisture levels, pH, temperature, and the presence of corrosive chemicals. By providing real-time data, corrosion sensors allow for early detection and intervention, reducing the risk of catastrophic failures.
One of the most widely used types of corrosion sensors is the electrical resistance (ER) sensor. ER sensors work by measuring the change in electrical resistance of a thin metal element that corrodes at the same rate as the structure being monitored. As the metal element corrodes, its resistance increases, providing a direct measure of the corrosion rate.
2. Wireless Sensor Networks
The advent of wireless sensor networks (WSNs) has further enhanced corrosion monitoring capabilities. WSNs consist of multiple interconnected sensors that communicate wirelessly, allowing for the monitoring of large structures or geographically dispersed assets. These networks can transmit data in real-time to a central monitoring system, where it can be analyzed and used to inform maintenance decisions.
Wireless sensors are particularly useful for monitoring hard-to-reach areas, such as the interior of pipelines or the underside of bridges. Additionally, the use of wireless technology reduces the need for extensive cabling, making installation easier and more cost-effective.
3. Smart Coatings with Embedded Sensors
A recent innovation in corrosion monitoring involves the development of smart coatings embedded with sensors. These coatings not only protect the underlying material from corrosion but also provide real-time data on the condition of the coating and the material. For example, smart coatings can detect the presence of moisture or corrosive agents and transmit this information to a monitoring system.
Smart coatings with embedded sensors are particularly advantageous in harsh environments, such as offshore platforms or chemical processing plants, where traditional sensors may be difficult to deploy. These coatings offer a dual benefit of corrosion protection and monitoring, reducing the need for frequent inspections.
Predictive Analytics in Corrosion Monitoring
While sensors provide valuable real-time data on corrosion, the true potential of corrosion monitoring lies in the application of predictive analytics. Predictive analytics involves the use of data, statistical algorithms, and machine learning techniques to predict future events based on historical data. In the context of corrosion monitoring, predictive analytics can be used to forecast corrosion rates, identify patterns, and optimize maintenance schedules.
1. Data Collection and Integration
The first step in predictive analytics is the collection and integration of data from multiple sources. This includes data from sensors, historical inspection records, environmental conditions, and material properties. By integrating data from various sources, predictive analytics can provide a comprehensive understanding of the factors influencing corrosion and identify trends that may not be apparent from individual data points.
2. Machine Learning Algorithms
Machine learning algorithms are a key component of predictive analytics. These algorithms can analyze large datasets to identify patterns and correlations that may be indicative of future corrosion. For example, machine learning models can be trained to recognize the early signs of corrosion based on sensor data, allowing for proactive maintenance before significant damage occurs.
Several types of machine learning algorithms can be applied to corrosion monitoring, including regression models, decision trees, and neural networks. Each of these algorithms has its strengths and limitations, and the choice of algorithm depends on the specific application and the available data.
3. Predictive Maintenance
One of the most significant benefits of predictive analytics in corrosion monitoring is the ability to implement predictive maintenance strategies. Predictive maintenance involves using data-driven insights to anticipate when maintenance should be performed, rather than relying on fixed schedules or reactive repairs. This approach can significantly reduce maintenance costs, minimize downtime, and extend the lifespan of assets.
For example, in the oil and gas industry, predictive maintenance can be used to schedule pipeline inspections and repairs based on the predicted corrosion rates. This not only reduces the risk of leaks and spills but also optimizes the allocation of resources, ensuring that maintenance is performed only when necessary.
4. Risk Assessment and Decision-Making
Predictive analytics also plays a crucial role in risk assessment and decision-making. By analyzing data on corrosion rates, environmental conditions, and material properties, predictive models can estimate the probability of failure and the potential consequences. This information can be used to prioritize maintenance activities, allocate resources, and make informed decisions about asset management.
For instance, predictive analytics can help infrastructure managers determine which bridges are at the highest risk of corrosion-related failures and should be inspected or repaired first. This data-driven approach enables more effective risk management and ensures that critical infrastructure remains safe and reliable.
The Future of Corrosion Monitoring
As technology continues to advance, the field of corrosion monitoring is likely to see further innovations that enhance the accuracy, efficiency, and cost-effectiveness of corrosion management.
1. Integration with IoT and Cloud Computing
The integration of corrosion monitoring systems with the Internet of Things (IoT) and cloud computing is expected to play a significant role in the future. IoT-enabled sensors can collect and transmit data in real time to cloud-based platforms, where it can be analyzed and accessed from anywhere in the world. This connectivity allows for continuous monitoring and remote diagnostics, reducing the need for on-site inspections and enabling faster response times.
2. Advanced Materials and Nanotechnology
Advances in materials science and nanotechnology are also likely to influence the future of corrosion monitoring. For example, the development of nanomaterials with self-healing properties could lead to coatings that not only protect against corrosion but also repair themselves when damaged. Additionally, nanotechnology could enable the creation of more sensitive and precise sensors that can detect corrosion at the molecular level.
3. Artificial Intelligence and Autonomous Systems
Artificial intelligence (AI) and autonomous systems are poised to revolutionize corrosion monitoring. AI-powered systems can analyze vast amounts of data in real time, identify patterns, and make decisions without human intervention. Autonomous drones and robots equipped with corrosion sensors could be deployed to inspect large or difficult-to-access structures, such as offshore platforms or high-rise buildings, reducing the need for manual inspections and improving safety.
Conclusion
Corrosion monitoring has come a long way from traditional methods like visual inspections and ultrasonic testing to the use of advanced sensors and predictive analytics. These innovations have significantly improved the ability to detect and manage corrosion, enhancing safety, reduced costs, and extended asset lifespans.
As the field continues to evolve, the integration of IoT, AI, and nanotechnology promises to further revolutionize corrosion monitoring, making it more accurate, efficient, and proactive. By embracing these cutting-edge technologies, industries can better protect their assets, reduce environmental impact, and ensure the safety and reliability of critical infrastructure.