Corrosion Inhibitors: How They Work And Their Applications
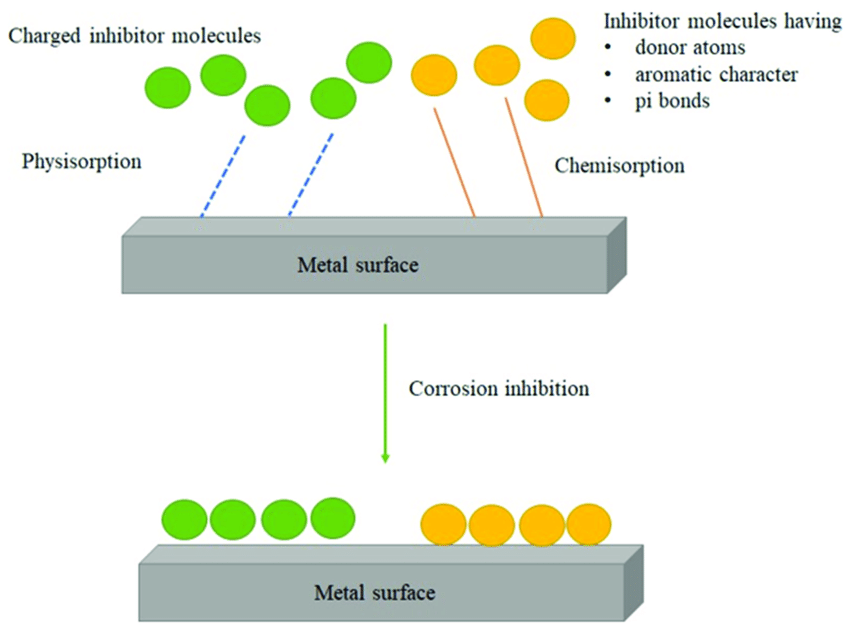
Corrosion is a natural and relentless process that leads to the degradation of materials, particularly metals, as they react with their environment. This process can cause severe damage to infrastructure, machinery, and various industrial equipment, leading to substantial financial losses and, in some cases, catastrophic failures. To mitigate the effects of corrosion, industries employ various strategies, one of the most effective being the use of corrosion inhibitors.
Corrosion inhibitors are chemical substances that, when added in small concentrations to an environment, significantly reduce the rate of corrosion. These inhibitors play a crucial role in extending the life of metal components, minimizing maintenance costs, and ensuring the safe and efficient operation of industrial systems. In this blog post, we will delve into the mechanisms by which corrosion inhibitors work, the different types of corrosion inhibitors, their applications across various industries, and the factors influencing their effectiveness.
Understanding Corrosion: A Brief Overview
Before exploring corrosion inhibitors, it is essential to understand the basics of corrosion. Corrosion is an electrochemical process that involves the transfer of electrons from a metal to its environment. This process typically occurs in the presence of an electrolyte, such as water, that facilitates the movement of ions. The metal surface acts as an anode, where oxidation occurs, while a reduction reaction takes place at the cathode. The most common example of corrosion is the rusting of iron, where iron reacts with oxygen and moisture to form iron oxide (rust).
The corrosion process can be influenced by various factors, including the type of metal, the composition of the electrolyte, temperature, pH levels, and the presence of corrosive agents such as chlorides. Given the complexity of these factors, controlling corrosion is a challenging task. This is where corrosion inhibitors come into play, offering a practical and cost-effective solution to slow down or prevent the corrosion process.
How Corrosion Inhibitors Work
Corrosion inhibitors function by interfering with the chemical reactions that cause corrosion. Their primary mode of action is to either:
-
Form a Protective Barrier: Corrosion inhibitors can form a thin, protective film on the surface of the metal. This barrier prevents corrosive agents from reaching the metal surface, thereby reducing the rate of corrosion.
-
Passivate the Metal Surface: Some inhibitors work by altering the electrochemical characteristics of the metal surface, making it less reactive and less susceptible to corrosion. This process is known as passivation.
-
Reduce the Corrosive Environment: Corrosion inhibitors can also work by modifying the environment to make it less corrosive. For example, they may neutralize acidic environments, thus reducing the tendency for metal dissolution.
-
Inhibit Cathodic and Anodic Reactions: Inhibitors can slow down or prevent either the anodic or cathodic reactions involved in the corrosion process. This reduces the overall rate of corrosion.
Types of Corrosion Inhibitors
Corrosion inhibitors are classified into different types based on their chemical composition, the mechanism by which they inhibit corrosion, and their application. The main types of corrosion inhibitors include:
1. Anodic Inhibitors
Anodic inhibitors, also known as passivating inhibitors, work by forming a protective oxide film on the surface of the metal. This film passivates the anodic sites, reducing the rate of metal dissolution. Anodic inhibitors are particularly effective in environments where localized corrosion, such as pitting, is a concern.
Common Examples:
-
Chromates: Chromates are widely used in industrial applications, especially in cooling systems and water treatment, to passivate steel and aluminum surfaces.
-
Nitrites: Nitrites are commonly used in reinforced concrete to protect steel rebar from corrosion. They form a passive oxide layer on the steel, preventing chloride-induced corrosion.
Application Considerations:
-
Anodic inhibitors must be used in sufficient concentrations to ensure complete coverage of the metal surface. Insufficient concentration can lead to localized corrosion, such as pitting.
-
Overuse of anodic inhibitors can sometimes lead to the formation of thick, non-adherent films that may spall off, exposing the metal to corrosive agents.
2. Cathodic Inhibitors
Cathodic inhibitors work by reducing the rate of the cathodic reaction, which typically involves the reduction of oxygen or the evolution of hydrogen. By slowing down the cathodic reaction, these inhibitors decrease the overall corrosion rate. Cathodic inhibitors are often used in conjunction with anodic inhibitors for comprehensive corrosion protection.
Common Examples:
-
Phosphates: Phosphates are widely used in water treatment to inhibit the cathodic reaction and prevent scale formation. They work by forming a protective film on the metal surface.
-
Zinc Salts: Zinc salts are commonly used in cooling systems as cathodic inhibitors. They work by precipitating zinc hydroxide on the cathodic sites, reducing the availability of oxygen for the reduction reaction.
Application Considerations:
-
Cathodic inhibitors are often used in environments where oxygen reduction is the primary cathodic reaction, such as in cooling towers and closed-loop water systems.
-
Proper dosing is crucial to avoid the formation of excessive deposits that could interfere with heat transfer or fluid flow.
3. Mixed Inhibitors
Mixed inhibitors, as the name suggests, affect both anodic and cathodic reactions. They provide a balanced approach to corrosion inhibition by passivating the metal surface and reducing the overall corrosion rate. Mixed inhibitors are versatile and can be used in a wide range of environments.
Common Examples:
-
Benzotriazole (BTA): Benzotriazole is a popular mixed inhibitor used to protect copper and its alloys. It forms a protective film on the metal surface, reducing both anodic and cathodic reactions.
-
Silicates: Silicates are used in water treatment to protect steel, aluminum, and other metals. They work by forming a thin, protective layer on the metal surface, inhibiting corrosion.
Application Considerations:
-
Mixed inhibitors are often the preferred choice in complex environments where both anodic and cathodic reactions are of concern.
-
The effectiveness of mixed inhibitors can be influenced by the specific environmental conditions, such as pH, temperature, and the presence of other chemicals.
4. Volatile Corrosion Inhibitors (VCIs)
Volatile corrosion inhibitors (VCIs) are compounds that can vaporize and form a protective layer on metal surfaces in enclosed spaces. VCIs are particularly useful for protecting metals during storage and transportation, where direct application of inhibitors may not be practical.
Common Examples:
-
Amine Carboxylates: These are widely used VCIs in the packaging of metal parts and equipment. They release vapor that condenses on metal surfaces, forming a protective layer.
-
Nitrites: Nitrite-based VCIs are used to protect steel and cast iron components during storage. They vaporize and deposit a thin, protective layer on the metal surface.
Application Considerations:
-
VCIs are ideal for use in enclosed environments, such as packaging, storage containers, and sealed compartments.
-
The effectiveness of VCIs depends on the tightness of the enclosure and the ability of the vapor to reach all metal surfaces.
5. Organic Inhibitors
Organic inhibitors are compounds containing carbon atoms that adsorb onto the metal surface, forming a protective film that prevents corrosion. These inhibitors are widely used in industries such as oil and gas, where they are added to fluids to protect pipelines and equipment from corrosion.
Common Examples:
-
Amines: Amines are commonly used in the oil and gas industry to protect carbon steel pipelines from corrosion. They form a hydrophobic film on the metal surface, reducing contact with corrosive agents.
-
Imidazolines: Imidazolines are another class of organic inhibitors used in the oil and gas industry. They are particularly effective in protecting steel in acidic environments.
Application Considerations:
-
Organic inhibitors are often used in environments where water and oil are present, such as in oilfield applications.
-
The effectiveness of organic inhibitors can be influenced by the chemical composition of the fluid and the temperature.
6. Inorganic Inhibitors
Inorganic inhibitors are compounds that do not contain carbon atoms and work by forming a protective layer on the metal surface or by altering the corrosive environment. These inhibitors are commonly used in water treatment, cooling systems, and industrial processes.
Common Examples:
-
Silicates: Silicates are widely used in cooling systems and water treatment to protect metals such as steel and aluminum. They form a protective film on the metal surface.
-
Molybdates: Molybdates are used as corrosion inhibitors in cooling systems and boilers. They work by forming a passivating oxide layer on the metal surface.
Application Considerations:
-
Inorganic inhibitors are often preferred in industrial applications where high temperatures and aggressive chemicals are present.
-
The effectiveness of inorganic inhibitors can be influenced by the concentration of the inhibitor and the composition of the environment.
Applications of Corrosion Inhibitors
Corrosion inhibitors are used across a wide range of industries and applications to protect metals from corrosion. Some of the key applications include:
1. Oil and Gas Industry
The oil and gas industry is one of the largest users of corrosion inhibitors. Corrosion is a significant concern in this industry due to the presence of water, carbon dioxide (CO2), hydrogen sulfide (H2S), and other corrosive agents in the production and transportation of oil and gas. Corrosion inhibitors are used to protect pipelines, drilling equipment, storage tanks, and refineries.
Applications:
-
Pipeline Protection: Corrosion inhibitors are added to the fluid inside pipelines to protect the inner surface from corrosion. Organic inhibitors, such as amines and imidazolines, are commonly used in this application.
-
Drilling Fluids: Corrosion inhibitors are added to drilling fluids to protect drilling equipment from corrosion caused by acidic conditions and high temperatures.
-
Storage Tanks: Corrosion inhibitors are used in storage tanks to protect the metal surface from corrosion caused by the stored product, such as crude oil or refined petroleum products.
2. Water Treatment
Corrosion is a significant concern in water treatment systems, including cooling towers, boilers, and potable water systems. Corrosion inhibitors are used to protect metal components, such as pipes, heat exchangers, and storage tanks, from corrosion caused by water and dissolved salts.
Applications:
-
Cooling Systems: Corrosion inhibitors, such as phosphates and silicates, are added to cooling water to protect metal surfaces from corrosion and scale formation.
-
Boiler Water Treatment: Corrosion inhibitors are used in boiler water treatment to protect the metal surfaces of boilers and heat exchangers from corrosion caused by high temperatures and dissolved oxygen.
-
Potable Water Systems: Corrosion inhibitors are used in potable water systems to protect pipes and storage tanks from corrosion. Inhibitors such as silicates and phosphates are commonly used in this application.
3. Automotive Industry
Corrosion inhibitors are widely used in the automotive industry to protect metal components from corrosion caused by exposure to moisture, salts, and other corrosive agents. Inhibitors are used in cooling systems, fuel systems, and as additives in lubricants and coatings.
Applications:
-
Cooling Systems: Corrosion inhibitors are added to engine coolant to protect the metal surfaces of the cooling system, including the radiator, engine block, and water pump, from corrosion.
-
Fuel Systems: Corrosion inhibitors are added to gasoline and diesel fuels to protect fuel system components, such as fuel injectors and fuel tanks, from corrosion caused by water and other contaminants.
-
Coatings and Lubricants: Corrosion inhibitors are used as additives in coatings and lubricants to protect metal surfaces from corrosion and wear.
4. Aerospace Industry
Corrosion inhibitors play a critical role in the aerospace industry, where the protection of aircraft components from corrosion is essential for safety and performance. Inhibitors are used in coatings, sealants, and as additives in hydraulic fluids and fuels.
Applications:
-
Coatings and Sealants: Corrosion inhibitors are added to coatings and sealants used on aircraft surfaces to protect the metal from corrosion caused by exposure to moisture, salts, and atmospheric pollutants.
-
Hydraulic Fluids: Corrosion inhibitors are added to hydraulic fluids used in aircraft systems to protect metal components, such as pumps, valves, and actuators, from corrosion and wear.
-
Fuel Additives: Corrosion inhibitors are added to aviation fuels to protect fuel system components from corrosion caused by water and other contaminants.
5. Construction Industry
Corrosion inhibitors are used in the construction industry to protect metal structures, such as bridges, buildings, and pipelines, from corrosion caused by exposure to moisture, salts, and other environmental factors. Inhibitors are used in concrete, coatings, and as additives in construction materials.
Applications:
-
Concrete: Corrosion inhibitors are added to concrete to protect embedded steel reinforcement from corrosion caused by chloride ions and other corrosive agents.
-
Coatings: Corrosion inhibitors are used in coatings applied to metal structures, such as bridges and buildings, to protect the metal from corrosion caused by exposure to moisture and atmospheric pollutants.
-
Construction Materials: Corrosion inhibitors are added to construction materials, such as steel and aluminum, to protect the metal from corrosion during fabrication, transportation, and installation.
Conclusion
Corrosion inhibitors are a critical component in the fight against corrosion, offering a practical and cost-effective solution to protect metal surfaces from degradation. Their ability to form protective barriers, passivate metal surfaces, and alter the corrosive environment makes them indispensable in various industries, including oil and gas, water treatment, automotive, aerospace, and construction.
The effectiveness of corrosion inhibitors depends on several factors, including the type of inhibitor, the environmental conditions, and the specific application. By understanding the different types of corrosion inhibitors and their mechanisms of action, industries can make informed decisions to select the most appropriate inhibitor for their needs, ensuring the longevity and reliability of their assets.
As technology continues to advance, the development of new and more effective corrosion inhibitors will play a crucial role in addressing the challenges of corrosion in increasingly complex and demanding environments. Whether in protecting critical infrastructure, enhancing the safety and performance of vehicles and aircraft, or ensuring the integrity of pipelines and storage tanks, corrosion inhibitors will remain at the forefront of corrosion prevention and control.