Corrosion In Marine Environments: Challenges And Solutions
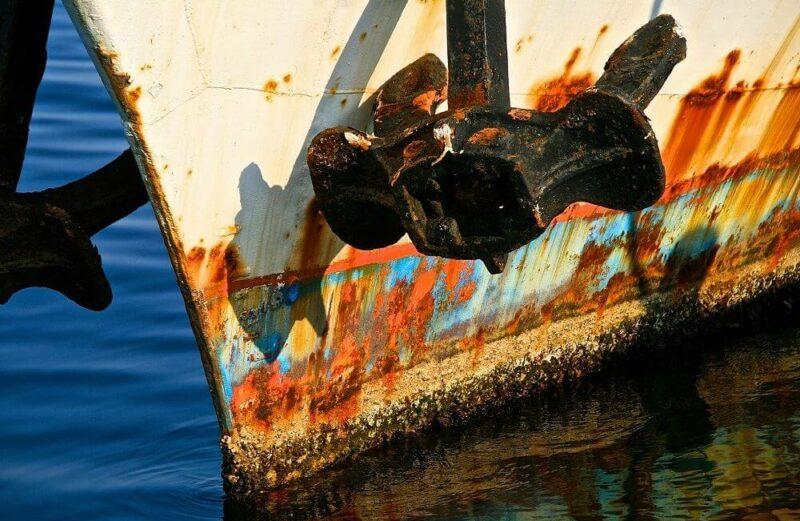
Corrosion in marine environments is a significant challenge faced by industries that rely on structures and equipment exposed to seawater and other harsh marine conditions. From offshore oil platforms to ships, ports, and coastal infrastructure, corrosion can lead to structural failures, costly repairs, and significant economic losses. The unique combination of saltwater, oxygen, temperature variations, and biological factors creates an aggressive environment that accelerates the corrosion process, making it a critical issue for industries and governments alike.
In this blog post, we will explore the nature of corrosion in marine environments, the challenges it presents, and the various solutions available to mitigate its impact. We will also discuss the latest advancements in corrosion prevention technologies and the importance of ongoing research and development in this field.
Understanding Corrosion in Marine Environments
Corrosion is an electrochemical process that involves the deterioration of metals as they react with their environment. In marine environments, this process is exacerbated by several factors that make these conditions particularly corrosive:
-
Saltwater: Seawater contains high concentrations of dissolved salts, primarily sodium chloride (NaCl). The presence of chloride ions (Cl-) is especially problematic as they are highly aggressive and can penetrate protective oxide layers on metal surfaces, accelerating corrosion.
-
Oxygen: Oxygen dissolved in seawater is another key factor in the corrosion process. It promotes the oxidation of metals, leading to the formation of rust and other corrosion products. The availability of oxygen varies with depth and water movement, influencing the rate of corrosion.
-
Temperature: Temperature variations in marine environments can affect the rate of corrosion. Warmer temperatures generally increase the rate of chemical reactions, including corrosion. Additionally, temperature changes can lead to thermal expansion and contraction of materials, potentially causing stress and cracking.
-
pH Levels: The pH of seawater is typically slightly alkaline, with an average pH of around 8.1. However, local variations in pH, caused by factors such as pollution or biological activity, can influence the rate of corrosion. Lower pH levels (more acidic conditions) tend to increase the aggressiveness of corrosion.
-
Biological Factors: Marine organisms, such as bacteria, algae, and barnacles, can contribute to corrosion through a process known as microbiologically influenced corrosion (MIC). These organisms can form biofilms on metal surfaces, creating localized environments that promote corrosion.
-
Mechanical Stress: Structures in marine environments are often subjected to mechanical stresses, such as wave action, currents, and the weight of the structure itself. These stresses can cause cracks and other defects in materials, which can act as initiation points for corrosion.
Challenges of Corrosion in Marine Environments
The challenges of corrosion in marine environments are multifaceted and can have severe consequences if not adequately addressed. Some of the key challenges include:
1. Structural Integrity
Corrosion can compromise the structural integrity of marine infrastructure, such as ships, offshore platforms, bridges, and pipelines. As metals corrode, they lose strength and thickness, leading to potential failures. This is particularly concerning for critical structures that are essential for safety and operation.
For example, corrosion on an offshore oil platform can weaken load-bearing components, increasing the risk of structural failure and environmental disasters. Similarly, corrosion in pipelines can lead to leaks, posing safety hazards and environmental risks.
2. Economic Impact
The economic impact of corrosion in marine environments is substantial. The cost of repairing or replacing corroded structures and equipment can be enormous, especially in remote or difficult-to-access locations. In addition to direct repair costs, there are also indirect costs, such as production downtime, environmental cleanup, and increased insurance premiums.
In the shipping industry, for example, corrosion can lead to increased maintenance costs and reduced vessel lifespan. This, in turn, can affect shipping companies' profitability and competitiveness.
3. Environmental Concerns
Corrosion in marine environments can have significant environmental consequences. For example, the corrosion of pipelines and storage tanks can lead to oil spills, contaminating the ocean and coastal ecosystems. The release of corroded metal particles and other pollutants can also harm marine life and disrupt ecological balance.
Additionally, the disposal of corroded materials, such as ships and offshore platforms, poses environmental challenges. The recycling and disposal of these materials must be carefully managed to minimize their impact on the environment.
4. Safety Risks
Corrosion poses serious safety risks, particularly in industries where human lives are at stake. For instance, corrosion in offshore platforms or ships can lead to catastrophic failures, endangering the lives of workers and passengers. The integrity of marine infrastructure, such as bridges and ports, is also critical for public safety.
Moreover, corrosion in pipelines carrying hazardous substances, such as oil or natural gas, can lead to explosions, fires, and toxic releases, posing significant safety risks to nearby communities and the environment.
Solutions for Corrosion in Marine Environments
To address the challenges of corrosion in marine environments, a combination of preventive measures, protective technologies, and regular maintenance is essential. The following are some of the key solutions used to combat corrosion in marine settings:
1. Protective Coatings
One of the most effective methods for preventing corrosion in marine environments is the application of protective coatings. These coatings act as a barrier between the metal surface and the corrosive elements in seawater, such as chloride ions and oxygen.
Types of Protective Coatings:
-
Paints: Marine-grade paints, often containing anti-corrosive pigments, are commonly used to protect metal surfaces from corrosion. These paints form a physical barrier that prevents moisture and oxygen from reaching the metal.
-
Epoxy Coatings: Epoxy coatings are widely used in marine applications due to their excellent adhesion, chemical resistance, and durability. They provide a strong barrier against corrosion and are often used on ship hulls, offshore platforms, and pipelines.
-
Polyurethane Coatings: Polyurethane coatings offer good flexibility and abrasion resistance, making them suitable for structures subjected to mechanical stress. They are often used in combination with epoxy coatings for enhanced protection.
-
Metallic Coatings: Metallic coatings, such as zinc, aluminum, or nickel, can be applied to metal surfaces through processes like galvanization, electroplating, or thermal spraying. These coatings provide sacrificial protection, as the coating material corrodes preferentially, protecting the underlying metal.
2. Cathodic Protection
Cathodic protection is a technique used to prevent corrosion by converting the metal structure into the cathode of an electrochemical cell. This can be achieved through two main methods: galvanic (sacrificial anode) cathodic protection and impressed current cathodic protection (ICCP).
-
Galvanic Cathodic Protection: In this method, a more reactive metal (sacrificial anode) is attached to the metal structure. The sacrificial anode corrodes instead of the protected metal, providing corrosion protection.
-
Impressed Current Cathodic Protection (ICCP): ICCP systems use an external power source to drive a continuous current to the metal structure, preventing corrosion. Inert anodes are used in ICCP systems, providing long-term protection for large and complex structures.
Cathodic protection is widely used in marine environments to protect structures such as ship hulls, offshore platforms, pipelines, and harbor facilities. It is particularly effective when used in conjunction with protective coatings.
3. Material Selection
The selection of corrosion-resistant materials is another critical factor in preventing corrosion in marine environments. Materials such as stainless steel, titanium, and high-nickel alloys are commonly used in marine applications due to their excellent resistance to corrosion.
For example, stainless steel is often used in the construction of marine vessels, offshore structures, and pipelines due to its resistance to rust and pitting in seawater. Titanium and high-nickel alloys are used in more aggressive environments where resistance to both corrosion and mechanical stress is required.
In addition to metallic materials, non-metallic materials such as fiberglass-reinforced plastics (FRP) and composites are increasingly being used in marine applications. These materials are inherently resistant to corrosion and are suitable for use in pipelines, tanks, and other structures exposed to seawater.
4. Corrosion Inhibitors
Corrosion inhibitors are chemical compounds that can be added to the environment to slow down or prevent the corrosion process. In marine environments, corrosion inhibitors can be used in cooling water systems, ballast water tanks, and other areas where metal surfaces are in contact with seawater.
Corrosion inhibitors work by forming a protective film on the metal surface, blocking the interaction between the metal and corrosive agents. They can be used in combination with other corrosion prevention methods, such as coatings and cathodic protection, to enhance overall protection.
5. Regular Inspection and Maintenance
Regular inspection and maintenance are essential to ensure the continued effectiveness of corrosion prevention measures in marine environments. Inspections should include visual assessments, non-destructive testing (NDT), and monitoring of cathodic protection systems.
Maintenance activities may include cleaning and recoating surfaces, replacing sacrificial anodes, and repairing damaged areas. Early detection and repair of corrosion damage can prevent more severe problems and extend the lifespan of marine structures.
6. Innovative Technologies
Advancements in technology are providing new tools and methods for combating corrosion in marine environments. Some of the latest innovations include:
-
Smart Coatings: Smart coatings are designed to respond to environmental changes, such as temperature or pH, by releasing corrosion inhibitors or self-healing when damaged. These coatings offer enhanced protection and reduce the need for frequent maintenance.
-
Remote Monitoring Systems: Remote monitoring systems use sensors and data analytics to continuously monitor the condition of marine structures. These systems can detect early signs of corrosion, allowing for timely intervention and reducing the risk of catastrophic failures.
-
Nano-Coatings: Nano-coatings are ultra-thin coatings that offer superior protection against corrosion by creating a highly impermeable barrier. These coatings are being developed for a wide range of marine applications, including ship hulls, offshore platforms, and underwater pipelines.
Conclusion
Corrosion in marine environments presents significant challenges that can have serious economic, environmental, and safety implications. However, with the right combination of preventive measures, protective technologies, and ongoing maintenance, it is possible to mitigate the impact of corrosion and ensure the long-term durability and safety of marine structures.
The use of protective coatings, cathodic protection, corrosion-resistant materials, and corrosion inhibitors are all essential components of an effective corrosion prevention strategy. In addition, regular inspection and maintenance, combined with the adoption of innovative technologies, can help to reduce the risk of corrosion-related failures.
As industries continue to operate in increasingly harsh marine environments, the importance of ongoing research and development in corrosion prevention cannot be overstated. By staying at the forefront of technological advancements and best practices, industries can continue to protect their assets, reduce costs, and safeguard the environment.