Cathodic Protection: Techniques And Applications In Industry
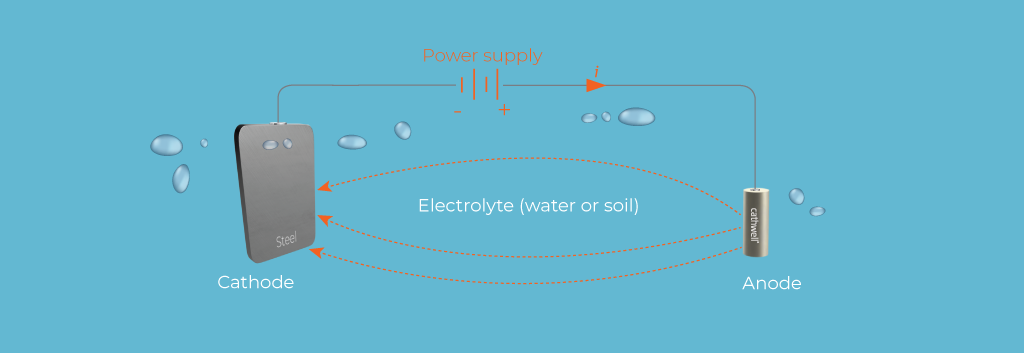
Corrosion is a pervasive issue that can lead to the premature failure of metals in various industrial applications. It is particularly concerning in industries where metal structures are exposed to harsh environments, such as underground pipelines, offshore platforms, and storage tanks. One of the most effective methods for combating corrosion is cathodic protection (CP). This technique has been widely used for decades to protect metal structures from corrosion, extending their lifespan and ensuring their structural integrity.
In this blog post, we will explore the principles of cathodic protection, the different techniques used in its application, and the various industries that rely on CP to protect their assets. We will also discuss the advantages and challenges associated with cathodic protection and its future in the industry.
Understanding Cathodic Protection
Cathodic protection is a method used to prevent corrosion on metal surfaces by making the metal surface the cathode of an electrochemical cell. This is achieved by either applying a small, continuous electric current to the metal structure or by using a more easily corroded metal to act as the anode. By doing so, the metal structure, now the cathode, is protected from corrosion.
The basic principle behind cathodic protection is to control the electrochemical reactions that cause corrosion. In an unprotected metal, corrosion occurs when the metal acts as the anode in an electrochemical cell, losing electrons and undergoing oxidation. By converting the metal to a cathode, cathodic protection prevents the loss of electrons and, therefore, the corrosion process.
Types of Cathodic Protection
There are two main types of cathodic protection systems: Galvanic (Sacrificial Anode) Cathodic Protection and Impressed Current Cathodic Protection (ICCP). Both systems are based on the same principle but use different methods to achieve cathodic protection.
1. Galvanic (Sacrificial Anode) Cathodic Protection
Galvanic cathodic protection, also known as sacrificial anode protection, involves attaching a more reactive metal, known as a sacrificial anode, to the metal structure that needs protection. The sacrificial anode, being more electrochemically active, corrodes preferentially, thereby protecting the cathodic metal structure.
How It Works:
-
Anode Selection: The sacrificial anode is usually made of a metal such as zinc, magnesium, or aluminum, which has a higher electronegativity than the protected metal. When connected to the metal structure, the anode corrodes instead of the metal, providing protection.
-
Electrochemical Reaction: The sacrificial anode donates electrons to the metal structure, preventing it from corroding. The anode gradually deteriorates over time as it corrodes, and it needs to be replaced periodically to maintain protection.
Advantages:
-
Simple Installation: Galvanic cathodic protection systems are relatively simple to install and do not require an external power source.
-
Low Maintenance: These systems are generally low-maintenance and operate automatically once installed.
-
Effective in Isolated Areas: Galvanic CP is particularly effective in areas where access to power is limited or where minimal maintenance is preferred.
Disadvantages:
-
Limited Protection Area: The protection area is limited by the distance between the anode and the metal structure. Large structures may require multiple anodes.
-
Anode Replacement: The sacrificial anodes eventually corrode and must be replaced, which can increase long-term maintenance costs.
Applications:
-
Underground Pipelines: Galvanic CP is commonly used to protect underground pipelines from soil corrosion.
-
Marine Structures: It is also used in marine environments to protect ships, offshore platforms, and other submerged structures.
-
Storage Tanks: Aboveground and underground storage tanks often utilize galvanic CP to prevent corrosion.
2. Impressed Current Cathodic Protection (ICCP)
Impressed Current Cathodic Protection (ICCP) involves the use of an external power source to drive a continuous electric current from an inert anode to the metal structure that needs protection. Unlike galvanic CP, which relies on the natural potential difference between the anode and the cathode, ICCP systems actively control the current to provide protection.
How It Works:
-
Power Supply: ICCP systems use a rectifier to convert alternating current (AC) to direct current (DC), which is then applied to the metal structure.
-
Inert Anodes: The anodes used in ICCP systems are typically made of inert materials such as titanium coated with mixed metal oxides (MMO), platinum, or graphite. These anodes do not corrode and have a long service life.
-
Controlled Current: The current supplied by the rectifier is carefully controlled to ensure that the metal structure remains cathodic and protected from corrosion.
Advantages:
-
Extensive Coverage: ICCP systems can protect large structures and complex geometries, as the current can be adjusted to ensure uniform protection.
-
Long-Term Protection: The use of inert anodes means that the system can provide long-term protection with minimal maintenance.
-
Adjustable Current: The ability to control the current allows for precise protection in varying environmental conditions.
Disadvantages:
-
Higher Initial Cost: ICCP systems typically have higher upfront costs due to the need for a power source and more complex installation.
-
Maintenance: The system requires regular monitoring and maintenance to ensure proper operation, including checking the rectifier and anode connections.
-
Power Dependency: ICCP systems rely on a continuous power supply, which can be a drawback in remote areas or during power outages.
Applications:
-
Large Marine Structures: ICCP is widely used to protect large marine structures such as ships, offshore platforms, and pipelines.
-
Bridges: Steel-reinforced concrete bridges often use ICCP to protect the embedded steel from corrosion caused by environmental exposure.
-
Industrial Plants: ICCP systems are commonly used in industrial plants to protect process equipment, storage tanks, and pipelines.
Applications of Cathodic Protection in Industry
Cathodic protection is an essential technique in various industries where metal structures are exposed to corrosive environments. The following are some of the key industries that rely on CP to protect their assets:
1. Oil and Gas Industry
The oil and gas industry is highly susceptible to corrosion due to the harsh environments in which it operates, including offshore platforms, pipelines, and refineries. Cathodic protection is widely used to protect critical infrastructure in this industry.
-
Pipelines: Underground and subsea pipelines are protected using both galvanic and ICCP systems to prevent corrosion caused by soil, water, and other environmental factors. CP systems are critical in preventing leaks, ruptures, and costly repairs.
-
Offshore Platforms: Offshore platforms are exposed to highly corrosive seawater, making them vulnerable to corrosion. ICCP systems are commonly used to protect the steel structures of these platforms, ensuring their long-term integrity.
-
Storage Tanks: Aboveground and underground storage tanks used in the oil and gas industry are often protected using cathodic protection to prevent corrosion caused by moisture, chemicals, and soil conditions.
2. Marine Industry
The marine industry faces some of the most challenging corrosion conditions due to constant exposure to seawater, salt spray, and humidity. Cathodic protection is essential for protecting ships, offshore structures, and other marine equipment from corrosion.
-
Ships: Both galvanic CP and ICCP systems are used to protect the hulls of ships from corrosion. ICCP is particularly effective for large vessels, providing uniform protection over the entire hull surface.
-
Offshore Structures: Offshore oil platforms, wind turbines, and other marine structures rely on cathodic protection to prevent corrosion and ensure their structural integrity. ICCP systems are commonly used due to their ability to provide long-term protection in harsh marine environments.
-
Harbors and Docks: Harbor facilities, including piers, docks, and mooring systems, are protected from corrosion using cathodic protection. This ensures the longevity of these structures, which are constantly exposed to seawater.
3. Water and Wastewater Industry
The water and wastewater industry uses cathodic protection to protect infrastructure such as pipelines, storage tanks, and treatment facilities from corrosion.
-
Water Pipelines: Underground water pipelines are vulnerable to corrosion due to soil conditions and the presence of moisture. Cathodic protection systems, particularly galvanic CP, are used to prevent leaks and extend the lifespan of these pipelines.
-
Wastewater Treatment Plants: Steel tanks, piping, and equipment in wastewater treatment plants are protected using cathodic protection to prevent corrosion caused by the aggressive chemical environment within these facilities.
-
Reservoirs and Storage Tanks: Water reservoirs and storage tanks are often protected using ICCP systems to prevent corrosion caused by water and environmental exposure. This is critical in ensuring the safety and reliability of the water supply.
4. Infrastructure and Transportation
Cathodic protection is also widely used in infrastructure and transportation to protect steel-reinforced concrete structures, bridges, and tunnels from corrosion.
-
Bridges: Steel-reinforced concrete bridges are susceptible to corrosion caused by environmental factors such as moisture, salt, and pollution. ICCP systems are commonly used to protect the embedded steel reinforcement from corrosion, ensuring the long-term durability of the bridge.
-
Tunnels: Tunnels, particularly those constructed with steel-reinforced concrete, are protected from corrosion using cathodic protection. This is especially important in tunnels exposed to water infiltration and deicing salts.
-
Parking Structures: Steel-reinforced concrete parking structures are often exposed to moisture, salts, and chemicals, making them vulnerable to corrosion. Cathodic protection systems are used to protect the steel reinforcement and extend the lifespan of these structures.
5. Power Generation Industry
The power generation industry, including nuclear, coal, and renewable energy facilities, relies on cathodic protection to protect critical infrastructure from corrosion.
-
Cooling Water Systems: Cooling water systems in power plants are susceptible to corrosion due to the constant presence of water and chemicals. Cathodic protection systems are used to protect steel pipes, tanks, and equipment from corrosion, ensuring the reliable operation of the cooling system.
-
Nuclear Power Plants: Nuclear power plants use cathodic protection to protect critical components such as storage tanks, piping, and reactor vessels from corrosion. This is essential in ensuring the safety and reliability of the plant.
-
Wind Turbines: Offshore wind turbines are exposed to harsh marine environments, making them vulnerable to corrosion. ICCP systems are commonly used to protect the steel structures of these turbines, ensuring their long-term operation.
Challenges and Future Trends in Cathodic Protection
While cathodic protection is highly effective in preventing corrosion, it also faces several challenges and opportunities for innovation. Some of the key challenges and future trends in cathodic protection include:
Challenges:
-
Monitoring and Maintenance: Cathodic protection systems require regular monitoring and maintenance to ensure their effectiveness. This can be time-consuming and costly, particularly for large and complex structures.
-
Power Dependency: ICCP systems rely on a continuous power supply, which can be a limitation in remote areas or during power outages. Ensuring reliable power sources is critical to the success of these systems.
-
Environmental and Regulatory Compliance: The use of certain materials in cathodic protection, such as lead-based anodes, can raise environmental and regulatory concerns. The industry is increasingly moving toward the development of environmentally friendly alternatives.
Future Trends:
-
Smart CP Systems: The development of smart cathodic protection systems that use sensors, data analytics, and remote monitoring to optimize performance and reduce maintenance requirements is an emerging trend. These systems can provide real-time data on the condition of the protected structure and automatically adjust the current to ensure optimal protection.
-
Sustainable Anode Materials: Research is ongoing into the development of more sustainable anode materials that are environmentally friendly and cost-effective. This includes the use of advanced composites, nanomaterials, and recycled metals.
-
Hybrid Protection Systems: The integration of cathodic protection with other corrosion prevention methods, such as coatings and inhibitors, is becoming more common. Hybrid protection systems offer a multi-layered approach to corrosion prevention, providing enhanced protection in challenging environments.
Conclusion
Cathodic protection is a proven and effective method for preventing corrosion in a wide range of industrial applications. By converting metal structures into cathodes, CP systems protect them from the damaging effects of corrosion, extending their lifespan and ensuring their structural integrity.
Both galvanic and impressed current cathodic protection systems offer unique advantages and are used in various industries to protect critical infrastructure. From underground pipelines and offshore platforms to bridges and power plants, cathodic protection plays a vital role in safeguarding assets from corrosion.
As technology continues to advance, the future of cathodic protection is likely to see the development of more efficient, sustainable, and smart systems that enhance the effectiveness of corrosion prevention. With the ongoing challenges of corrosion in modern industry, cathodic protection will remain a cornerstone of asset protection and reliability.